OGAWA WASHI
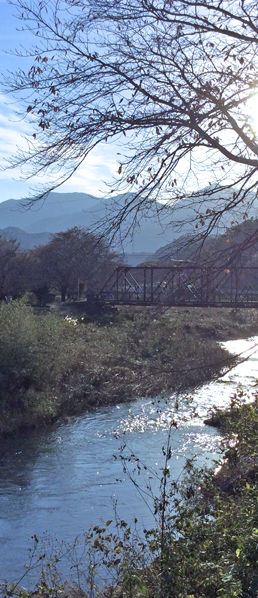
Ogawa Town and Higashi-chichibu Village are located at the heart of Saitama Prefecture, in the north-west of Tokyo, just a little over an hour train ride away, in a basin commanding a view of the outer Chichibu Mountains. The abundance of water from the Tsuki River that flows across the region has nurtured the paper making industry in the area.
Its paper making history dates back to the 8th century. In the late Edo period (1780~1867), demand for paper increased dramatically, making Ogawa area one of the largest paper producing regions.
It has also long been renowned as the washi industry location closest to Tokyo.
Handmade Ogawa Washi is carefully made, sheet by sheet, by the hands of skilled craftspeople.
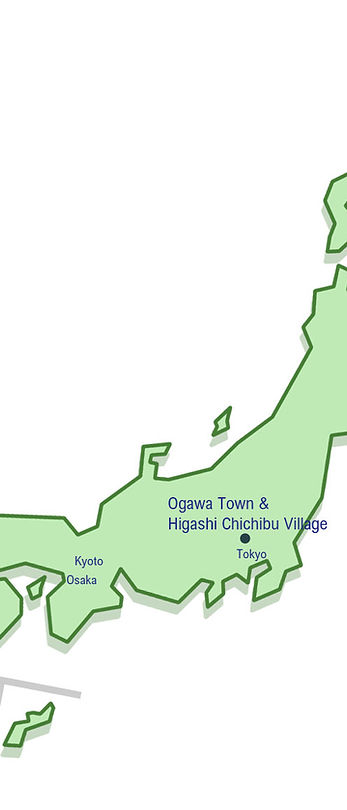
ROOTED IN TRADITION, DESIGNED FOR INNOVATION
Washi is still produced in many parts of Japan. Paper produced in Ogawa Town, Higashi-Chichibu Village, and nearby areas is collectively known as “Ogawa Washi.” Washi’s elegant translucence, subtly irregular texture, strength and durability make it suitable for countless practical and artistic applications. Rooted in centuries of tradition, washi may be the best possible material for creative explorations and innovation.

A MYRIAD APPLICATIONS. IMAGINATION’S THE LIMIT
Washi’s unique texture inspires warmth, making wonderful invitations and notecards. Because the fibers are left long and uneven, washi has incredible strength and is an ideal material for art works, interior design, conservation and repair. It is workable even when wet, an excellent quality for papier mâché and etching projects in which paper is soaked.
WARMTH, BODY, & STRENGTH
Kozo (paper mulberry) is native to Japan and is primarily used for making washi. Ascribed a masculine quality due to its thickness and strength, kozo is grown annually as a crop so no forests are depleted. Kozo's white inner bark is meticulously separated, cooked, cleaned, and pounded. Paper is painstakingly made on a bamboo screen, sun-dried on wooden boards and sorted, sheet by sheet.
TRANSLUCENT, ABSORBENT & FLEXIBLE
Kozo’s naturally translucent fibers allow the transmission of light, making it perfect for screen doors, lamps, shutters, and blinds. Washi readily absorbs inks and dyes, resulting in dense and vibrant colors, and responds well to embossing. Washi is crease-, wrinkle-, and tear-resistant and behaves almost like cloth, which is perfect for book covers and packaging.
LOW ACIDITY & UNIQUE
Traditionally made Japanese papers are acid-free. Bleached naturally, the washi does not turn yellow in sunlight but becomes whiter when struck by ultraviolet rays. Archival papers from Japan dating from 1000 years ago are still in pristine condition. With a broad range of patterns, textures and colors, washi gives a distinctive touch to any paper item.
*Click the image to see more information on Washi
HOSOKAWA-SHI
THE FINEST OF ALL OGAWA WASHI
Japanese Important Intangible Cultural Asset, 1987
UNESCO Intangible Cultural Heritage, 2014
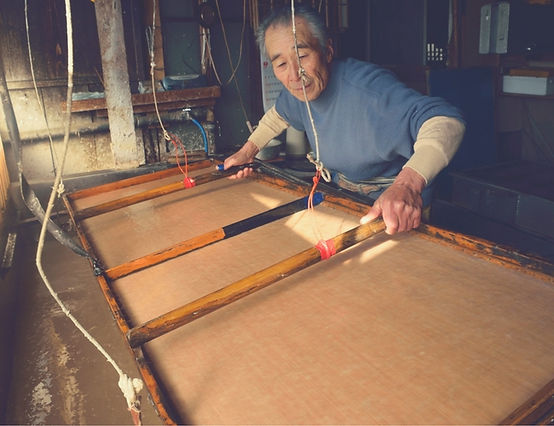
Hosokawa-shi is a durable, glossy, and water resistant paper used by Edo Period merchants for their account books.
It is an exemplar of all Ogawa Washi.
It is listed as a Japanese Important Intangible Cultural Asset in 1987,
and a UNESCO Intangible Cultural Heritage in 2014.
Hosokawa-shi is a durable, glossy, and water resistant paper used
by Edo Period merchants for their account books.
It is an exemplar of all Ogawa Washi.
In 1978, the Japanese Government recognized the innovative quality of this handmade paper, and the technique to make it was designated an Important Intangible Cultural Asset.
In 2014, the traditional technique of making Hosokawa- shi was one of 3 washi techniques
from Japan that UNESCO added to their list of Intangible Cultural Heritage
(the other two are Sekishu-banshi from Shimane Prefecture and Hon-mino-shi from Gifu Prefecture).
In order to maintain the unique texture of Hosokawa- shi,
only domestic kozo trees are used, and traditional methods and equipment
employed in the execution of the nagashi-suki method of sheet forming.




In contrast to handmade washi,
using machines enables mass production.

While sizes of handmade paper are limited, using machines allows making larger sizes of washi.
The general process for making milled washi is essentially the same as the handmade process.
There are now two factories producing milled washi in Ogawa Town. Making washi with machines is much faster and results in a more consistent quality finish than by hand. Being able to offer washi at low prices is particularly beneficial for fulfilling big orders of the paper.

Natural Wood Bits
Beige, Tan and Brown paper with mulberry wood bits, Amber paper with bamboo bits, Brown Paper with cedar bits,

Digital Washi Paper
Semi-Translucent,
Tanabata with Origami Flacks
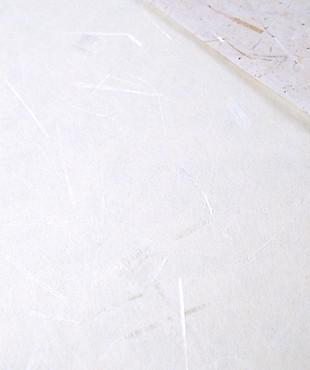
Tairei-shi
Tairei-shi can be amde in various colors. It is used for formal style stationery
and wrapping Kimono cloth.